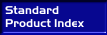
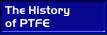
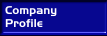
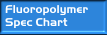
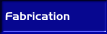
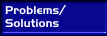
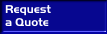
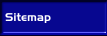
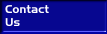
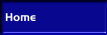
|
 |



Property
Comparison of Various Fluoropolymers
Property |
ASTM
test method/test condition |
PTFE |
PFA |
FEP |
ETFE |
CTFE |
|

Physical Properties
Specific
gravity |
D792
D570/24 hrs 1/2"t |
2.13~2.22 |
2.12~2.17 |
2.12~2.17 |
1.70~1.76 |
2.10~2.18 |
Water
absorption (%) |
|
<0.00 |
<0.03 |
<0.01 |
<0.1 |
<0.00 |
Mold
shrinkage (cm/cm) |
|
0.02
~0.05 |
0.04 |
0.03~0.06 |
0.03~0.04 |
0.015~0.020 |
Contact
angle (degree) |
Angle
to level |
110 |
115 |
115 |
96 |
84
|
|

Thermal Properties
 |
Thermal
conductivity (cal/sec/cm)
|
C177 |
6
X 10-4 |
|
6
X 10-4 |
5.7
X 10-4 |
4.7~5.3
X 10-4
|
Coefficient
of linear thermal expansion (1/°C) |
D696/23~60°C |
10
X 10-5 |
12
X 10-5
|
8.3~10.5
X 10-5 |
5~9
X 10-5 |
4.5
~ 7.0 X
10-5 |
Melting
point (°C) |
|
327 |
302~310 |
270 |
260 |
210~212 |
Melt
viscosity (coise)
|
|
10-11~10-13
(340-380°C) |
10-4~10-5
(380°C) |
4X10-4
~10-5
(380°C) |
10-4~10-5
(300-330°C) |
10-7
(23°C) |
Maximum
temp. for continuous use
(°C/°F)
|
|
260/500 |
260/500 |
200/392 |
150/302 |
120/248 |

Mechanical Properties
|
Tensile
strength
(kgf/cm2) |
D638/23°C
|
140~350 |
280~315 |
190~220 |
410~470 |
320~420 |
Elongation
(%) |
D638/23°C |
200~400 |
280~300 |
250~330 |
420~440 |
80~250 |
Compression
strength (kgf/cm2) |
D695/1%
deformation, 25°C |
50~60 |
50~60 |
50~60 |
109 |
90~120 |
Tensile
modulus
(kgf/cm2) |
D638/23°C |
4,000 |
|
3,500 |
5,000~8,000 |
10,500~21,000 |
Hexural
Modulus
(kgf/cm2) |
D790/23°C |
5,000~6,000 |
6,600~7,000 |
5,500~6,500 |
9,000~14,000 |
13,000~18,000 |
Impact
strength
(ft-lb/ln) |
D256/23°C
lzod |
3.0 |
|
No
breakdown |
No
breakdown |
2.5~2.7 |
Hardness
(Shore) |
Durometer |
D50~D65 |
D60 |
D55 |
D75 |
D90 |
Deformation
under load (%) |
D621/100°C
70 kfg/cm2,
24 hrs
D621/25°C
140 kgf/cm2,
24 hrs |
5.0

7.0
|
2.4

2.7
|
5.0

3.0
|
5.4

2.3
|
2.6

0.2
|
Static
friction coefficient |
Coated
steel surface |
0.20 |
0.50 |
0.50 |
0.60 |
0.80 |

Electrical Properties
|
Dielectric
constant |
D150/103Hz
D150/108Hz
|
2.1
2.1 |
2.1
2.1 |
2.1
2.1 |
2.6
2.6 |
2.3~2.7
2.3~2.5 |
Dielectric
dissipation factor |
D150/103HZ
D150/108HZ
|
<1
X 10-5
2 X 10-5 |
1
X 10-5
3 X 10-5 |
6
X 10-5
5 X 10-5 |
8
X 10-4
5 X 10-3 |
(2.3~2.7)
X10-2
1 X 10-2 |
Dielectric
breakdown
strength (V/ml) |
D149/Short
time, 1/8 in |
480 |
500 |
500~600 |
400 |
500 |
Volume
resistivity (ohm-cm) |
D257 |
>10-18 |
>10-18 |
>10-18 |
>10-18 |
>10-18 |
Chemical
resistance Weatherability Combustibility (%) |


D2863/Oxygen
concentration index |
Excellent

Excellent
>95 |
Excellent

Excellent
>95 |
Excellent

Excellent
>95 |
Excellent

Excellent
>31 |
Excellent

Excellent
>95 |

Typical
Filler Properties

|
Filler
|
Physical
Form
|
Amount
(% Weight)
|
Effect
of Filler
|
|
Glass
Fibers |
Milled
Fibers
|
up
to 40%
(also in combination with graphite, MoS2 and carbon)
|
- increased
compressive strength
- increased
rigidity
- increased
wear resistance
- reduced
cold flow
- resistant
to organic solvent
|
Carbon

Carbon
Fibers
|
Powder

Milled
Fibers
|
up
to 25%
(also in combination with graphite, bronze, and glass)
up to 30%
|
- increased comprehensive strength
- increased hardness
- increased wear resistance
- improved thermal conductivity
- good dry running properties
- electrically conductive at higher filler contents
- resistant to hydrofluoric acid
|
Graphite |
Powder
|
up
to 25%
(also in combination with glass, bronze, and carbon)
|
- improved
sliding properties
- reduced
coefficient of friction
- improved
thermal conductivity
|
Bronze |
Powder
|
up
to 60%
(also in combination with carbon, graphite, and MoS2))
|
- increased
comprehensive strength
- increased
hardness
- increased
wear resistance
- improved
thermal conductivity
- reduced cold flow
|
Molybdenum
disulphide (MoS2) |
Powder
|
up
to 5%
(also in combination with glass and bronze)
|
- improved
sliding properties
- increased
wear resistance
|
Stainless
Steel |
Powder
|
up
to 60%
|
- improved thermal conductivity
- reduced cold flow
- resistant to most chemicals
|
Pigments |
Powder
|
up
to 2%
|
- for coloring
(identification)
|
|